so they do last for generations
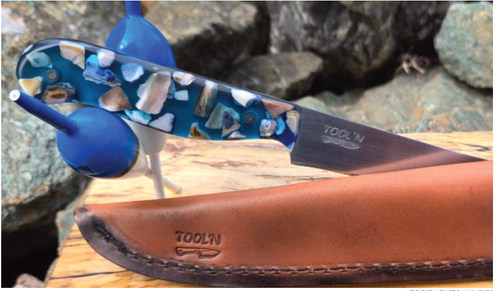
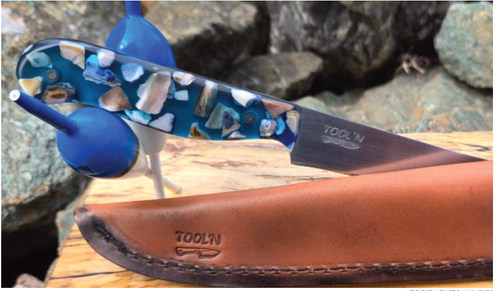
so they do last for generations,” he added.
Leonard uses a band saw or 4-inch grinder with a diamond blade to cut out a rough profile of the blade. Then he uses his 2-inch by 72-inch belt grinder/sander with various attachments to hone the piece down to what he wants. One of the attachments is a surface grinder he uses for the blades and handles.
“A lot of my wood is sourced locally and a lot of it is larger stock — 2 inches thick, an inch-and-a-half thick. I need a handle that is just a hair over a quarter-inch thick. So I’ll cut it with the band saw; then I’ll put it on that surface grinder to get it completely smooth and level on both sides, and to the thickness that I want.
“That was a big investment when I purchased the 2-by-72, but it was a game changer as far as what I could do and how long it took to do it.”
He said with his small grinder, it would take probably two hours to make the blade, but that time was reduced to 15 minutes with the 2-by-72 grinder. He can also be a lot more precise, especially when it comes to fine-tuning the taper of the blade.
“I’ll scribe a line down the center of the blade and work my way towards it. That when you look at it, both sides are equal. It’s symmetrical,” he said.
After he finishes the blade, it must be refined by fire. Leonard uses a heat-treating oven to change the molecular properties of the steel, increasing hardness and strength.
“Every steel has its own recipe, if you want to call it, to bring it up to a desired temperature, hold it there for a desired amount of time, and then take it up to its final temperature and hold it there for x amount of minutes, again depending on the steel,” said Leonard.
“When I first started, I used just a fire brick forge and that was fired with map torches. And the brick was kind of like what you’d line a fireplace with. I could do high-carbon steels and that was about it. And I started getting requests for steels that I could not use, so that’s why I got a heat treat oven that was made specifically for knives.”
After coming out of the heat treat oven, high carbon and stainless steels are handled differently. High carbon steel comes out of the oven at 1,500 degrees Fahrenheit. Leonard will immediately dunk it in a bucket of oil for seven or eight seconds to cool it. Then it goes into the tempering oven. The tempering process hardens the blade to prevent brittleness.
“Again with tempering, every steel is a little bit different. And depending on the hardness you want to get out of the steel, it’s a different temperature,” said Leonard.
The blade goes through multiple heating and cooling cycles, being allowed to cool off overnight in between cycles. Trying to expedite the process compromises the strength of the blade.
“I wanted to test that. So one of the blades I did, it was just a stock knife I was making. So I did the first temper cycle, let it cool the way it needed to, put it back in, and after the second tempering cycle, I wanted to keep working on it. I didn’t want to wait until the next day to let it cool down. So I figured, ‘Let’s try to cool it down.’ So I took the air hose and cooled it down so I could work on it. I did my test where I drove it into the plywood. No sooner I