started pushing it over
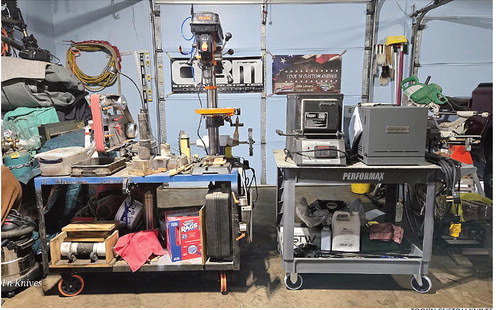
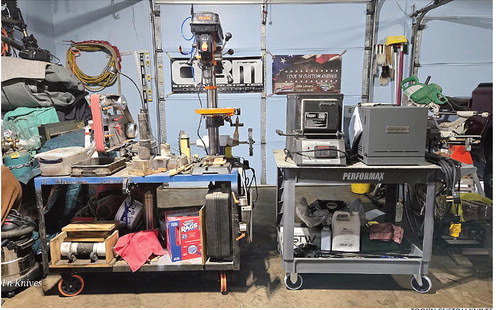
started pushing it over, I snapped the tip right off. I learned my lesson of ‘Well, I’m not going to short-cut it no more,’” said Leonard.
Stainless steel is handled differently. It must be initially heated to 2,000 degrees and held there for up to half an hour. After coming out of the heat treat oven, it does not get dunked into the oil. Instead, it is sandwiched between two 1-inch thick aluminum plates and Leonard blows air between the plates to cool it. It only takes a couple of minutes for the metal to go from 2,000 degrees to cool enough to handle. Then the blade goes through what is called cryogenic treatment. It is put in a freezer kept at -5 degrees for 24 hours. This binds the molecules in the metal together. When it comes out of the deep freeze, it’s ready for tempering like any other knife, using two-hour cycles.
After the blade is fully treated, Leonard attaches the handle, often customized with a special wood the customer requests. Leonard uses a variety of woods, mostly local, although he also uses specialty woods such as olive wood from Bethlehem, Israel. He uses pins to attach the blade to the handle — sometimes hidden, sometimes visible.
Once the handle is attached, he applies a coat of epoxy and lets it cure. He uses an industrial-grade epoxy which has a very high tensile strength, is UV resistant and water resistant. The recommended cure time for the epoxy is eight hours, or 24 hours if you want it to cure even harder.
“I always do the full 24 hours. That way I know it’s not going to fail,” said Leonard. “When I clamp the handle scales onto the blade, I’ll let it sit for 24 hours before I do anything with it.”
After that, Leonard does a final sanding to ensure a smooth finish. He then makes the sheath. He has made a variety of different designs, including sheaths with a woven look, created by using a leather stamping tool. Lastly, he sharpens the blade before presenting it to his customer.
In the process of making the knife, Leonard ends up with excess materials that he always tries to find a use for. Since a lot of his knives are hunting knives, they may have a piece of an antler for a handle and he uses the rest of the antler to make a knife display stand. He also uses extra antler pieces for bottle openers and back scratchers. Extra pieces of steel he uses as pendants for necklaces, He also makes his own conditioner for the leather and steel, using shea butter, beeswax, and lanolin. It can be used as lip balm because it’s all natural ingredients.
Every knife has a story One of Leonard’s favorite parts of his business is getting to hear the stories of what his clients intend to use their knife for.
“There’s stories behind a lot of ‘em and it makes me feel good to hear the story,” said Leonard.
He takes pride in combining functionality with artistry to create just the right item for each client.
“Probably one of the most unique knives I’ve made is on a tuna boat in New Jersey,” said Leonard. “The gentleman that I built it for got ahold of me. He owns a tuna boat