and wanted a fillet-style knife for cutting up his tuna
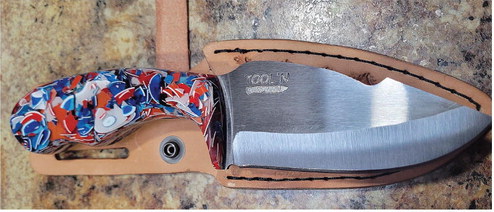
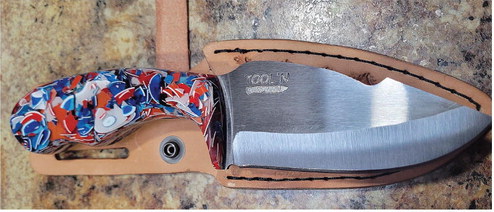
and wanted a fillet-style knife for cutting up his tuna. Normal fillet knives are pretty flimsy and have a real flexible blade, but he wanted a fillet knife that didn’t have as flexible of a blade. So I came up with it and made it for him. Knowing that it was going to be used on a boat for tuna, what I did for the handle is I bought some ground-up seashells and put them into a clear epoxy resin, and that’s what the handle was.
“Later he got ahold of me and said he wanted a blood knife. I said, ‘What is it?’ He said, ‘It’s a knife that you use for tunas. Behind their pectoral fin, they have a main artery. So what they do when they catch one is they want to bleed it out right away because that helps keep the meat fresher. So they don’t want to poke in too far because they don’t want the blood going into the meat. So just by having that short blade, they punch it in behind that artery and it bleeds out. I said, ‘Oh, I can make you one’ and put the same type of handle on.”
A lot of Leonard’s clients want a knife to give as a personalized gift for a friend or family member. For example, he made four matching knives for military buddies who were having stones placed at The Highground Veterans Memorial Park. The knives were identical, except each had their branch of service and nickname etched into the blade.
Leonard had another client from northern Minnesota who had an elk antler in his basement from an elk he shot 20 years ago. He asked for a knife with a handle from that antler and Leonard agreed.
“[My client] said, ‘It [the rack] has been in the basement a long time. It might not be very good.’ But anyway, he got it to me. I started taking a look at it and the antler was about shot. Antler is very hard. When I drill holes in it, it stinks to high heaven and is very hard to drill. But this one, I was able to take a pencil and push a hole through it because it was just that soft… I was able to salvage it for him. I dug out all of the junk out of there and filled it with epoxy. And that meant a lot to him because it was from an elk he had shot many years ago. And there was enough salvageable material that he had me make a knife for each one of his daughters.”
Sometimes Leonard is surprised with how people react to his work. As an example, one client requested a knife from Leonard and paid upfront for it, which isn’t the norm. Leonard asked him if he wanted to see pictures and videos of him working on the knife, and he said no. This surprised Leonard somewhat because normally people enjoy seeing the progress along the way. But, no matter. Leonard completed the knife and sheath and his client came to his house to pick it up.
“He’s looking and looking at the knife and not sayin’ much. And I was kind of worried he didn’t like it because he wasn’t saying much. I finally asked him, ‘Well, what do you think?’ And he started talking and his voice was breaking. He sounded like he was going to cry… I finally asked him, ‘What’s wrong?’ And he said, ‘I just love it.’ He was just so happy with it.
“So that was a very memorable moment. Again, there’s a story behind it. It might not have meant a lot to anyone else, but it meant a lot to me.”
Leonard can be found on Facebook, Instagram, and YouTube by searching “Tool’n Knives.” His YouTube channel includes videos of him showcasing the quality of his knives, whether that’s showing how clean a cut a knife can make, or pounding the tip of a knife into a piece of wood and then bending the knife forwards or backwards to see if the blade will snap.
“I used to watch the TV show, ‘Forged in Fire.’ And I thought, ‘I’m going to test my knives, just to make sure. If it’s going to have my name on it, I want to make sure it’s going to last and be tough,’” he said. “I have had people tell me, ‘Well, after I seen that video I wouldn’t hesitate to buy one of your knives.’ So I’ll keep doing them… People like watching and enjoying the process of how the knife is being built.”
Leonard can be reached at tooln98@gmail.com or by calling 715-316-2635.