Abby firms join COVID battle
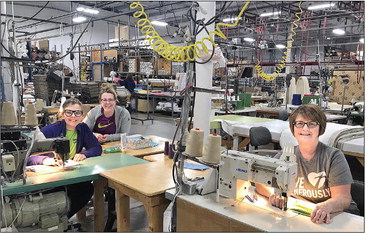
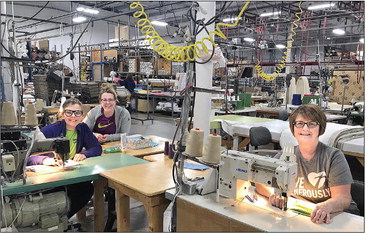
All Metal Stamping, DI, LLC retool to make masks, shields
With the nation facing an unprecedented public health crisis, two local manufacturing companies have retooled their operations to produce protective gear for those on the front lines of the battle against COVID-19.
DI, LLC (formerly Decorator Industries) is making thousands of cotton masks for medical workers, while All-Metal Stamping is about to start fabricating face shields that provide an extra layer of defense for doctors and nurses.
The owners of the two Abbotsford companies said they are happy to help out during a time of need by utilizing their unique manufacturing capabilities.
“We’re fortunate to be able to fill a need that’s out there, because we’re set up for it,” said Dan Hannula, owner of DI, LLC.
Ryan LaSee, owner of All Metal Stamping, said his company is making a mold for the plastic face shields this week, and is planning to make 11,300 of them on their first run next week.
“The medical workers are trying to preserve their N-95 masks, and this prevents the N-95s from being contaminated,” he said. “It helps with that.”
N-95 masks have received a lot of national attention in recent weeks, as they are in short supply. LaSee said the Marshfield Medical Center (MMC) is rationing the masks, giving each employee just one N-95 per week, so they all have to make them last.
LaSee said the idea came to him after he posted a Facebook message on March 20, asking his friends to identify a product he could make at All-Metal Stamping using some of his idle machinery.
“I got a couple of leads, but they were dead ends,” he said.
Then, he responded to a post from Rep. Bob Kulp (R-Stratford), who was asking companies to help with the coronavirus outbreak. Within minutes, LaSee said he was in contact with someone at MMC, who told him about the work being done by Dental Crafters, a Marshfield company that makes dental implants.
LaSee happens to be friends with the guys who run Dental Crafters, so he called them up.
“They had done all the leg work already,” he said. “They had been working with Marshfield, printing shields on 3-D printers.”
Since Dental Crafters already had an approved design, LaSee said “they made it incredibly easy for me to just fly into this thing, and start making it.”
The serendipity didn’t stop with La-See’s connection to Dental Crafters.
His sister runs AMS Bowfishing in Stratford, which happened to be starting a new fishing reel project that involves a mold base well-suited for making the face shield head gear using plastic injection.
LaSee said this cut his expenses by a lot because they can reuse the tooling.
“When the crisis is over, we’re going to pull the tooling out and use it for fishing gear,” he said.
All Metal Stamping is working on the mold this week and getting the tooling together, with the goal of starting full production next week.
“We should be able to run a tremendous amount of production, like a minimum of 120 headgears an hour,” he said. “It’s probably going to be closer to 200.”
LaSee said his company’s equipment is ideal for producing the face shields.
“I needed a product that was well suited for us, and this thing was perfect,” he said. “We’re really good at this type of thing.”
LaSee said he plans on donating some of the shields and selling others for slightly more than the cost of production. Besides MMC, he’s spoken to representatives of Prevea Hospital in Chippewa Falls, Clark County Health Center in Owen and Norwood in Marshfield.
All Metal Stamping normally makes products for the construction industry, which provided LaSee and his 47 employees with an exemption from the stayat- home order issued by the state. Even before the face shield project, he says his company’s workload has been steady.
“We do expect a slowdown at some point because job sites around the country are slowing down or stopping,” he said. “But we haven’t experienced that yet. We’re still busy.”
LaSee said the demand from local health care providers has been staggering, with an initial interest in over 50,000 masks.
“I would not be surprised if we will soon be at full production capacity of about 5,000 masks per day to meet demand,” he wrote in an email Monday.
As a business owner, LaSee said it’s hard to predict how long the need for these face shields will last.
“I’m concerned about the demand ending, and then subsequent overproduction,” he said. “It’s a really strange situation. It’s hard to gauge the demand.”
Still, LaSee said he’s impressed by how the “stars aligned” on this project, and he’s willing to take risks he doesn’t normally take.
“We didn’t even calculate our costs,” he said. “We were building the tooling and designing it before we even knew what we were going to have into it, which I’ve never done before.”
Making masks at DI
Just like LaSee, Dan Hannula at DI, LLC first got inspired to help out on March 20, when he heard about people making face masks on the East Coast. He went online to see exactly what they were making and then made a handful of his own prototypes that afternoon.
Hannula brought the masks home to his wife, a medical doctor who works at the state prison in Stanley.
“I tested them on her,” he said.
Based on his wife’s feedback, he made some tweaks to the design, went back to the office on Saturday morning, and placed a big order at JoAnne’s Fabrics in Wausau. After a conversation with someone at Marshfield Medical Center, some further research and final approval by his wife, Hannula was ready to massproduce the masks by Monday.
“We converted our production from bed spreads over to face masks,” he said. “It took us a half-day to move the machinery around. We got everything in place and got people trained. We started cutting and sewing in the afternoon on Monday.”
DI’s employees made 50 masks that first day, then ramped it up to 810 the following day. By Wednesday, they were up to 1,110, and on Thursday, the total run was 1,550. Friday, a half-day for workers, produced another 550.
By the end of the week, Hannula said they had produced between 3,700 and 3,800 masks.
“We distributed just about all that,” he said.
Hannula said DI is on pace to make about 170 masks per hour, or 1,500 every day. He’s been supplying them to MMC, with 2,800 going to their hospitals right away and then 400 per day after that.
Clark County Emergency Management also came and got 700 masks, and Sheila Nyberg from the Clark County Economic Development Corporation picked up 400 to be distributed at city halls, pharmacies and nursing homes. DI’s first shipment of 1,000 masks to the Wisconsin Department of Correction went out on Monday.
Hannula said his game plan is to provide the face masks locally at first and then branch out to the rest of Wisconsin so the state is prepared as COVID-19 cases continue to skyrocket.
“I don’t think there was anybody better suited to take this on, based on what we do,” he said. “It just so happens it’s right down our alley, and it was kind of a no-brainer to jump on this thing.”
Hannula said he is not charging for the masks at this point, and he believes other companies in his industry are doing the same.
Although they are not the same as the N-95s that hospitals are running short on, Hannula said the cotton masks DI is making block about 70 percent of most germs. Unfortunately, the coronavirus is 0.2 microns, which means the cotton masks can only keep out about 50 percent of those molecules, he said.
Hannula said they are adding a layer of flannel to boost the masks’ effectiveness by a few percentage points.
“Anything is better than nothing,” he said, noting that any type of mask helps keep people from touching their faces — a common way for people to contract the virus.
The N-95s may be the best at blocking the coronavirus, he said, but they are only supposed to be used once. They have other downsides, too, he said.
“My wife will tell you, as a doctor, they’re difficult to wear on an eight-hour shift,” he said. “They have to be sealed all around the face, and they’re difficult to breath through.”
The 100 percent cotton masks have their unique benefits, he said.
“It’s something we can provide, and it’s something that is reusable,” he said. “You can launder it and make use of it again.”
Hannula said he’s also been in discussions with MMC about possibly making other medical supplies, such as hospital gowns and hats.
DI normally fabricates window treatments and bed covers for the hospitality, health care and timeshare industries, but those have taken a back seat during the COVID-19 crisis. Hannula said he’s contacted all of his major customers and let them know that DI is temporarily converting its facility to make masks.
“Everybody was gracious enough to work with us by holding off on their orders, so we can focus on this issue right now,” he said. “Everybody’s here working full force; we’ve got everybody redirected into those areas.” Hannula said he’s impressed with how his 48 employees have stepped up to the task, and they actually feel a sense of competition with other companies that have switched to making masks.
DI is struggling to get some of the supplies it needs for the masks, especially elastic, which Hannula is ordering from China. However, local businesses are helping out by providing twist-ties that are used to seal the nose bridge on the masks. These are coming from bakeries, Abby County Market and the Cloverdale Country Store, he said.
Hannula said DI also got 200 yards of white elastic from someone in Dorchester — a perfect example of how it’s not just DI helping out, he noted.
“People are willing to contribute all the way across the board,” he said. “It’s serious stuff, and it’s kind of nice at this time in our country. To get away from this politics stuff is refreshing and seeing all the effort at the ground level.”
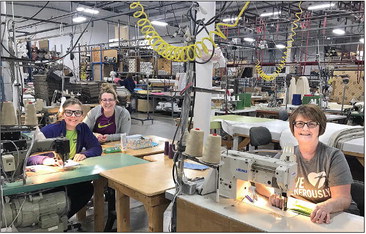
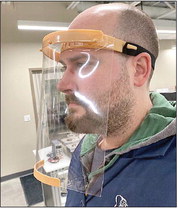
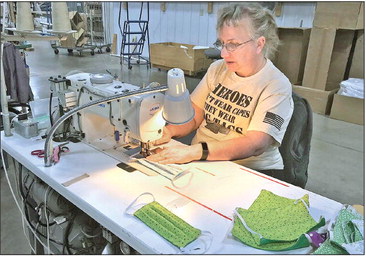
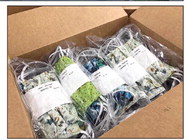
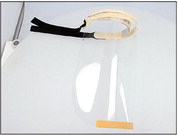